Surface acoustic wave (SAW) devices are used in many distinct application areas, which include electronics, microelectromechanical (MEMS) sensors or even microfluidic lab-on-a-chip (LoC) devices. The electrode geometry usually exhibits a narrow frequency band response – this can be directly utilized in radio frequency filters or oscillators. As the wavespeed of the acoustic wave propagating on the surface of a material is extremely sensitive to changes in material properties, such as temperature, pressure or mass loading due to foreign substances, SAW sensors can be designed for these modalities. Deformation and elongation of a cantilever structure changes propagation delay between a set of transducers – thus an accelerometer is realizable. Surface waves can be coupled into fluid-filled microchannels generating forces; a promising application for lab-on-a-chip devices.
A general SAW device comprises a piezoelectric substrate (usually crystalline materials, such as lithium noibate or lithium tantalate) and metal electrodes deposited on the surface as illustrated in the figure (referenced below):
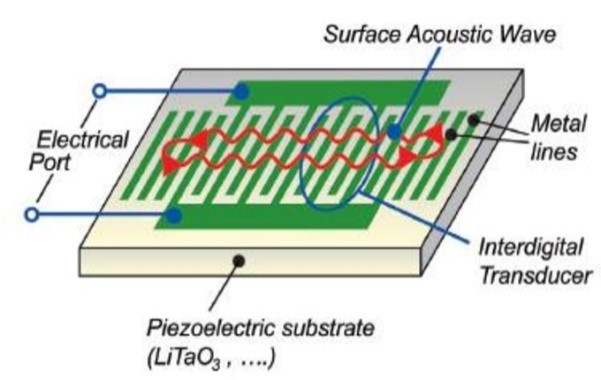
Electrical signals applied to the electrodes get converted into mechanical vibration due to the piezoelectricity of the substrate. This vibration propagates on the surface of the substrate.
Some of the commonly used electrode configurations are shown in the following figure (referenced below):
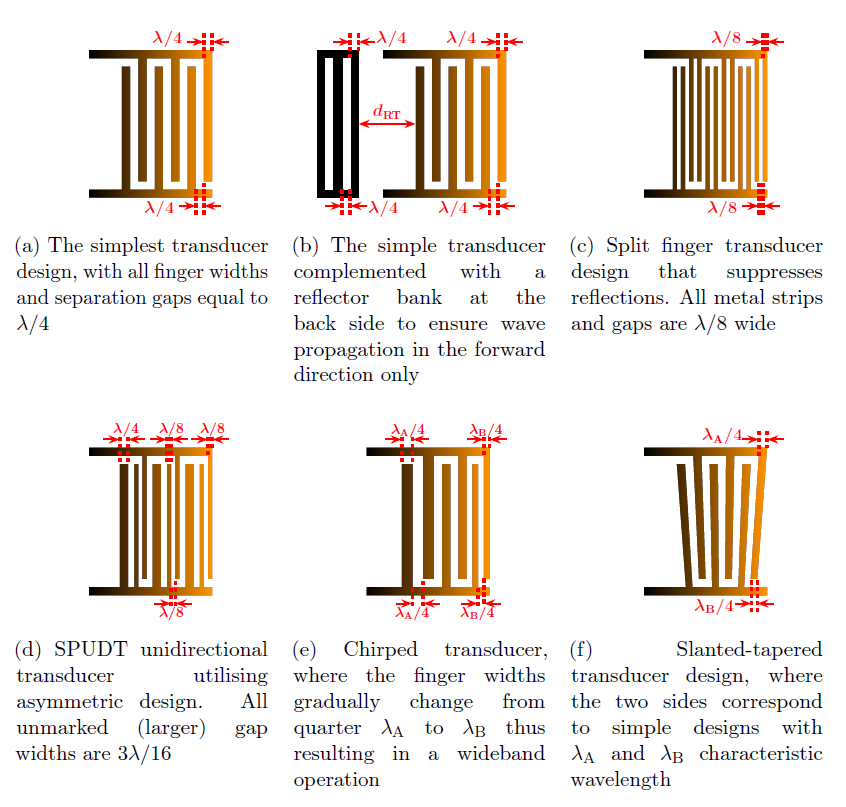
In the simplest case, all the electrode finger widths and gaps are uniformly a quarter of the operating wavelength [subfigure (a)]. This gives bidirectional, narrow band operation. Reflector structures behind the transducer [subfigure (b)] are utilized to entrap energy under the transducer, creating a resonator with high quality factor. Some more exotic transducer designs are also shown for wideband applications [(e), (f)].
When a unidirectional transducer is required – for delay lines or microfluidic applications – one can use a single-phase unidirectional transducer (SPUDT), here the electrode design allows for constructive interference of forward traveling waves, while suppresses backwards waves [(d)].
This operation can be verified using a 3D SAW unit cell (cross-reference OnScale models) and measuring the power flow through the left- and right-hand walls. As the model is periodic, it can be assumed the average of the two power flows is an overall ‘common mode’ power flow, while the difference can be viewed as the symmetric power flow. For example, as for a usual symmetric SAW unit cell the power through the two surfaces is antisymmetric (same magnitude but opposite sign), the overall power flow is almost zero as expected, so there is no net power flow in any direction. The model schematic in side view and power results are shown below:
![]() |
![]() |
However, for a SPUDT electrode configuration (see below for model schematic) there is a clear, non-zero amplitude and positive offset common mode power flow towards the positive x axis, meaning the transducer mainly directs energy along this direction as the following graph shows:
![]() |
![]() |
In this blog post, a brief overview of the commonly used surface acoustic wave transducer designs was provided with simulation results of a general symmetric SAW unit cell and an asymmetric SPUDT unit cell to verify the unidirectional power flow in the SPUDT design.